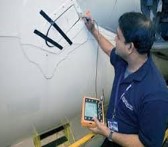
We also offer Pulsed Eddy Current (PEC) inspection technology for the detection of corrosion areas in carbon and low alloy steels. Measurements are taken through any non-conductive material e.g. insulation, protective coatings, concrete and marine growth.
Technique
It is an electromagnetic inspection technique used for measuring the thickness of steel objects, such as pipes and vessels, without the need for contact with the steel surface. This makes PEC very suitable for inspections where the surface of an object is not accessible. Readings are generated when a transmitter coil within a protective housing produces a magnetic pulse which induces eddy currents within the component wall. The eddy currents in turn produce a second magnetic pulse, which is detected by the receiving coil. The system monitors the rate of decay of the eddy current pulse within the steel wall and produces an average thickness value from the comparison of a calibrated signal. | ![]() |
Technique
- Provides the average remaining wall thickness measurement within the interrogated area (footprint).
- Direct contact is not required and wall thickness can be measured through any non-conductive material up to 200 mm thick, e.g. insulation material, paint, bitumen, dirt, ice or sludge
- Works through Stainless Steel and Aluminium sheeting less than or equal to 1mm.
- Surface preparation is not required enabling measurements to be taken through corrosion products
- Wide temperature range -100°C to 550°C
- Good reproducibility of PEC readings at the same locations makes it ideal for corrosion monitoring.
- Rope Access deployable
- Subsea and splash zone deployable
- Battery operated and robust design
- Fast and reliable data collection typically 700 to 1000 readings per day
Applications
- Vessel and pipe work inspection
- In-service corrosion/erosion monitoring
- Wall loss measurement through corrosion product
- Riser inspection above and below splash zones
- Storage tank inspection
- Ship hull surveys
- Refractory lined vessels
- Subsea Inspections